TYPICAL WIND ENERGY PROJECTS
GE RENEWABLE ENERGY – WIND BLADE STRUCTURAL ANALYSIS & TESTING
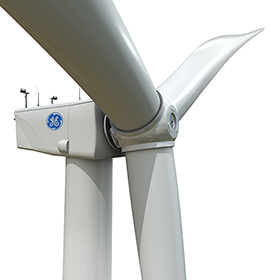
NSE Composites was contracted by General Electric (GE) Renewable Energy to develop static and fatigue analysis methods to predict failure in wind blade laminates and joints using composite damage mechanics and fracture mechanics. NSE Composites also supported GE Renewable Energy on wind turbine blade sub-article test design, test management, and analysis-test correlation.
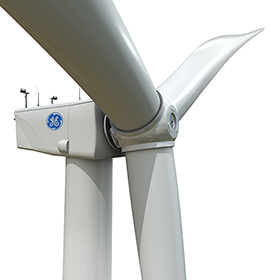
KNIGHT & CARVER – LWST WIND BLADE STRUCTURAL ANALYSIS
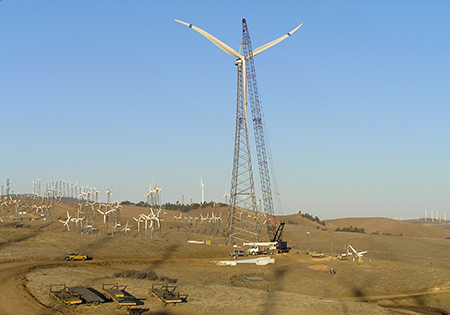
NSE Composites was contracted to provide structural analysis and finite element modeling for the development of Knight & Carver’s highly innovative wind turbine blade, known as the Sweep Twist Adaptive Rotor, or STAR blade. The new blade was designed to produce more electricity from a given wind turbine, without increasing wear and tear on the machine. Instead of the traditional linear shape, the blade features a curvature toward the trailing edge, which allows the blade to respond to turbulent gusts in a manner that lowers fatigue loads on the blade. The STAR blade is predicted to shed 20% of the root moment via a tip twist of nearly three degrees. The project was managed by Sandia National Laboratories. Other members of the design team were Dynamic Design, MDZ Consulting, and University of California, Davis. NSE Composites responsibilities on the project were:
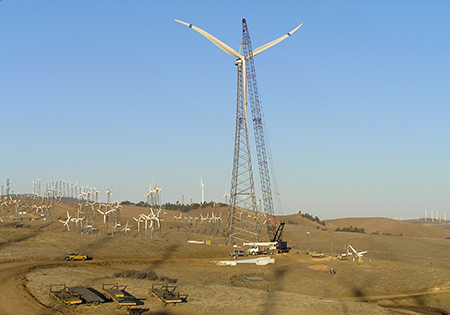
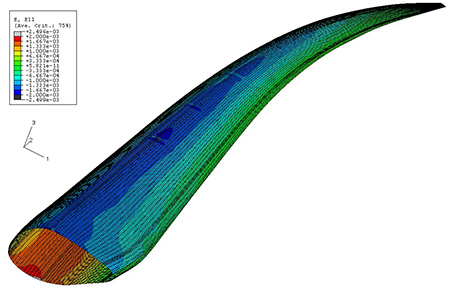
- Develop a finite element model (FEM) of the blade, including 3D effects and shear flows. A 3D solid model was generated in order to provide accurate twist predictions and avoid known issues with shell element offsets under torque loading.
- Confirm the twisting behavior predicted by beam analysis. The FEM twist predictions were in excellent agreement with the twist response measured during the full-scale static test.
- Generate equivalent beam properties for use in aerodynamics model (flap bending, edge bending, and torsional stiffness).
- Verify that the design meets basic strength and stiffness requirements. Both operating and extreme wind load cases were considered.
- Perform buckling/stability checks for given load cases, paying particular attention to the potential shear buckling due to the increased twist inherent in the design.
Read the Wind Blade Case Study article about this project.
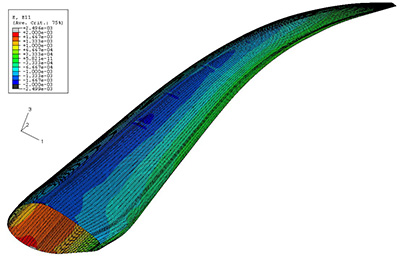