TYPICAL COMPOSITES R&D PROJECTS
SPIRIT AEROSYSTEMS – RAPID ANALYSIS TOOL FOR LARGE-NOTCH DAMAGE TOLERANCE
NSE Composites was contracted by Spirit AeroSystems to support the development of a stand-alone, rapid analysis tool for evaluating the residual strength of stiffened composite panels with a central notch severing one skin bay and a central stiffener (large notch). The objective of the project was to develop a closed-form analysis method for use during preliminary design of composite stiffened panels representative of commercial transport fuselage structures. The analysis tool was a Spirit deliverable to the NASA Advanced Composites Consortium (ACC).
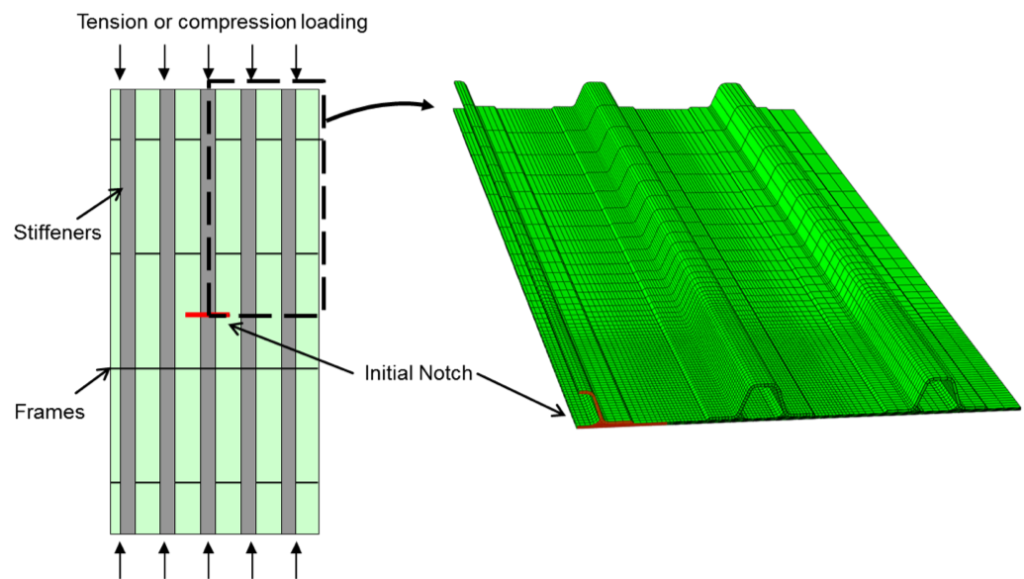
NSE’s approach for developing the tool included:
-
-
- Using progressive damage finite element (FE) analyses to capture all critical failure modes including skin damage growth, stiffener failure, and/or stiffener delamination.
- Comparing the predicted strength of stiffened panels to the strength of unstiffened panels to quantify the effect of the stiffeners and the associated damage growth arrestment.
- Evaluating a wide design space using a design-of-experiments (DOE) approach to evaluate variables such as skin and stiffener layup, stringer spacing, and stiffening ratio.
- Using the results of FE analyses to develop a physics-based closed-form response surface that can be used to rapidly predict the stiffened panel strength during preliminary design.
-
FOKKER AEROSTRUCTURES – STRINGER RUNOUT FATIGUE ANALYSIS
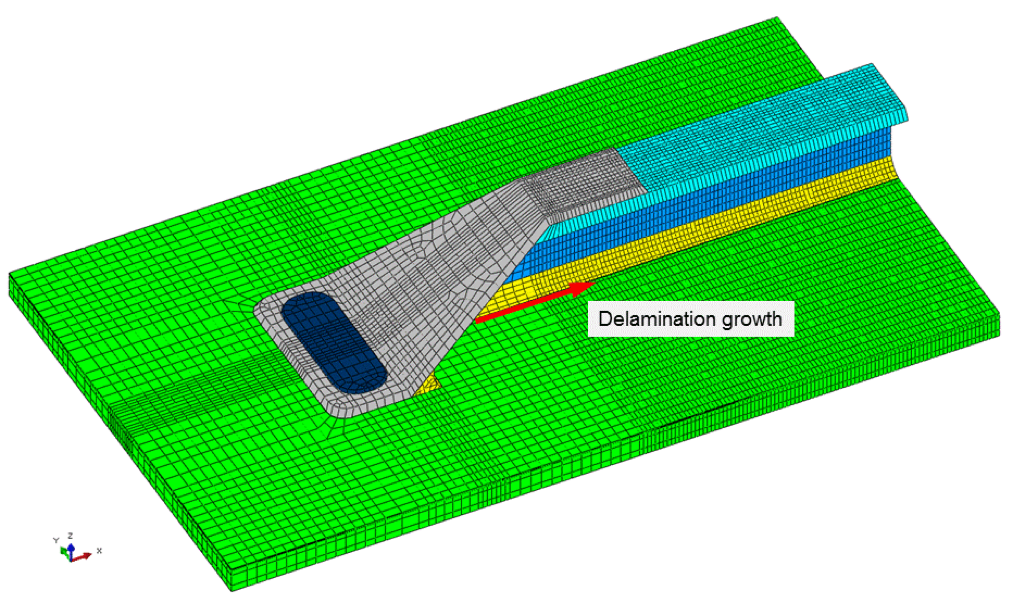
NSE Composites was contracted by Fokker Aerostructures to provide structural analysis of a stringer runout subjected to impact damage. The project was in support of the Thermoplastic Affordable Primary Aircraft Structure (TAPAS) program. Specific areas of support included:
-
-
- Finite element analysis of a 3-stringer test panel, which was tested after being impacted at the stringer runout to simulate in-service accidental damage. The skin and stringers were made from thermoplastic composite material (AS4/PEKK) and joined with a butt-joint connection between stringer web and skin.
- Fatigue delamination growth predictions of the post-impact damage state using fracture-mechanics-based analysis methods. The approach used the results from a detailed finite element model (FEM) together with fracture toughness coupon data to predict delamination growth under constant amplitude cyclic loading.
- Determination of fatigue delamination growth thresholds, development of load versus cycles (P vs. N) curves based on fatigue growth to an acceptable (i.e., non-detrimental) delamination size, and prediction of delamination growth direction.
- Test-Analysis correlation, including determining the “apparent” crack length by comparing the measured displacements and strains in the test to the predicted values from the FEM. This enabled mapping the complex internal crack state in the test (non-visible) to the simplified crack state modeled in the FEM.
-
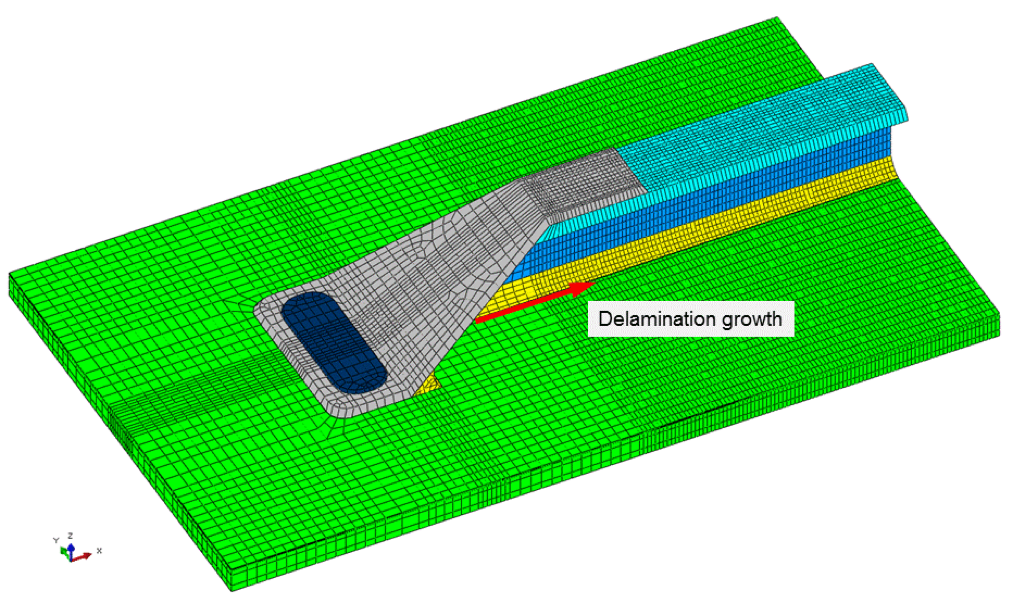
FOKKER AEROSTRUCTURES – FUSELAGE DAMAGE TOLERANCE ANALYSIS
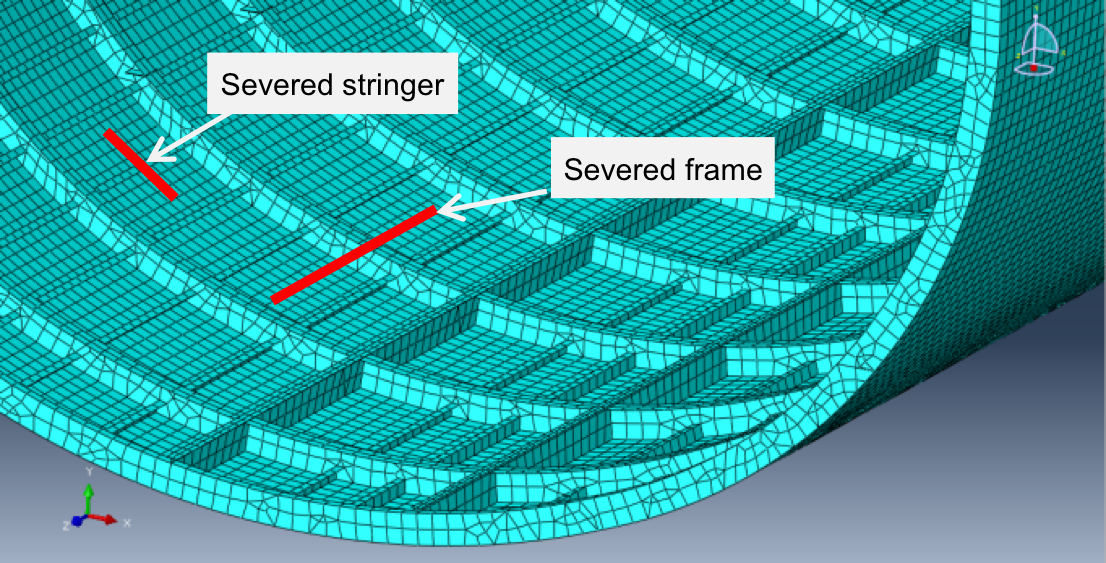
NSE Composites was contracted by Fokker Aerostructures to develop a damage tolerance analysis method for predicting the structural capability of an innovative thermoplastic (AS4/PEKK) fuselage panel with large damage. Critical damage scenarios for axial and hoop loading were considered in which a central stiffening member is severed to simulate large in-service damage. The project was in support of the Thermoplastic Affordable Primary Aircraft Structure (TAPAS) program. Specific areas of support included:
-
-
- Definition of a test program to characterize the large-notch strength of unstiffened composite panels under tension and compression loading to be used in the development of the analysis method. Testing of panels with integral stiffening elements was also defined to validate the ability of the analysis methodology to predict the onset of damage growth in different stress states.
- Development of a point strain analysis methodology in which the strain at a characteristic distance, “D0”, in front of a notch is used to predict the large-notch strength capability of structure. Using finite element modeling (FEM), the effects of structural configuration (e.g., stiffeners, curvature) are accounted for in the FEM strain predictions at the notch tip, thus allowing the strain at D0 determined from large notch tests of flat unstiffened panels to be used directly for strength predictions of configured structure.
-
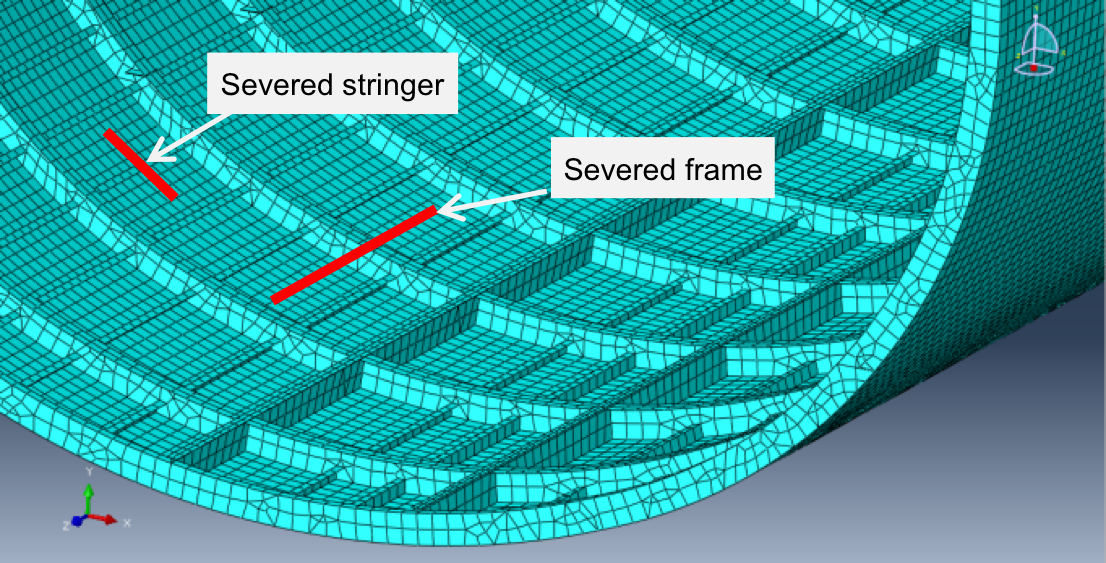
BOEING – CAI INTERFACE ELEMENTS
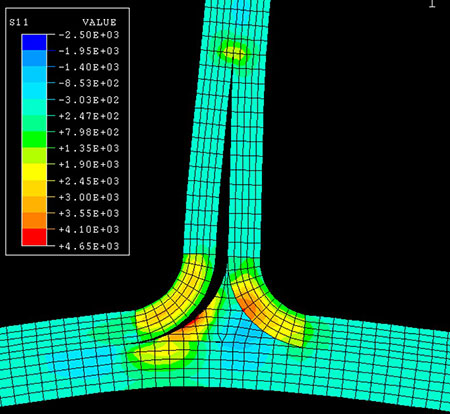
NSE Composites provided support to Boeing and the Composites Affordability Initiative (CAI) in the development and validation of interface fracture elements for the simulation of composite delamination onset and growth. Boeing developed an ABAQUS user element that implements the Virtual Crack Closure Technique (VCCT) in a novel way where both the critical release force and the energy consumed during strain softening is calculated based on fracture mechanics criteria.
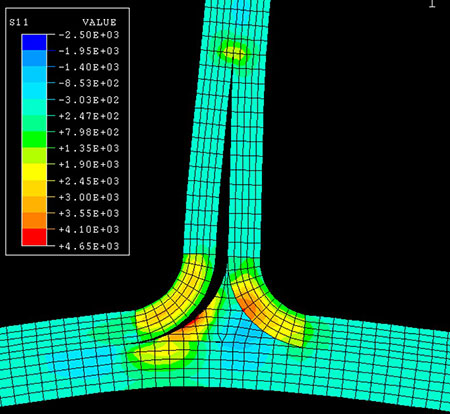
NSE performed work to validate the interface element over a range of structural configurations. Results were compared with closed-form solutions as well as with test data, when available. NSE also helped to extend the interface element technology to predict damage growth under cyclic loading (fatigue). The resulting implementation enables the use of the VCCT interface element to perform either fatigue onset analysis or progressive interlaminar fatigue growth analysis.
BR&T – AUSTRALIA: STRUCTURAL ANALYSIS AND OPTIMIZATION TOOLS
NSE Composites was contracted by Boeing Research & Technology-Australia (BR&T-A) to provide engineering support related to the enhancement of analysis and optimization tools for composite structures. Specific areas of support included:
-
-
- Development and validation of structural analysis methods for strength and buckling stability of skins, stiffeners, and spars.
- Implementation of structural analysis methods into existing optimization software.
-
BELL HELICOPTER – INTERLAMINAR FATIGUE ANALYSIS
NSE performed detailed analysis and finite element modeling to predict the strength and fatigue life of a developmental bonded composite structure. The purpose of this work was to apply the analytical methods previously developed under an Small Business Innovation Research (SBIR) project (A98-029) to assess damage initiation and growth due to static and fatigue loading in the selected areas of the structure.
Generalized plane strain finite element models were used to determine the stresses and strains in the adhesive and the composite laminates. Strength-of-materials failure criteria were then used to predict critical damage initiation loads and locations. Fracture mechanics methods were used to predict static strength and fatigue life based on fracture toughness and crack growth rate test data.
The strength-of-materials analysis identified three critical locations for damage initiation: 1) fiber failure in the hat radius, 2) delamination of the bulkhead flange on either side of the outer glass/epoxy ply, and 3) disbond/fracture of the adhesive fillet between the hat and bulkhead flange.
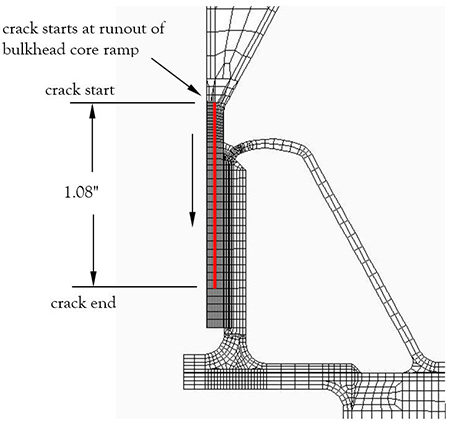
Fracture mechanics methods were then used to assess the static strength of the test article. A single crack path at the midplane of the bulkhead edgeband was chosen for the analysis. The crack was introduced into the model through the use of duplicate nodes and constraint equations which were progressively released. The model was run for a series of crack lengths to generate strain energy release rates as the crack was opened to a length of 1.08″. Total strain energy release rate (Gtot) and mode mix (GII/ Gtot) vs. crack length were calculated. The multiple load steps from the non-linear FEM provided Gtot data at several load levels for each crack length. Assessment of static strength and crack stability as a function of crack length were made by comparing Gtot from the model to critical fracture toughness test data (Gtot, crit) at the appropriate mode mix. The analysis showed that the predicted failure load is well above the test article failure load and that a crack or flaw is not predicted to grow at this interface at or below this load.
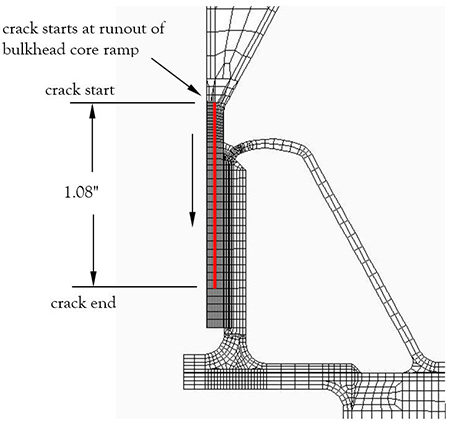
The onset of delamination due to fatigue loading was then evaluated at the same interface in the bulkhead edgeband. The peak value of Gtot over the length of the crack was calculated at the maximum cyclic fatigue load using the Gtot vs. crack length data from the FE model. This G value was then compared to Gonset vs. N data to assess the number of cycles before the onset of delamination.
BELL HELICOPTER – OPEN HOLE COMPRESSION STRENGTH
NSE Composites performed a series of research and development projects for Bell Helicopter using progressive damage analysis and empirical methods to develop a practical analysis tool for predicting the open hole compression strength of graphite laminated composites.
Abstract
BELL HELICOPTER – FATIGUE ANALYSIS
NSE Composites performed an R&D contract for Bell Helicopter Textron Inc. to help Bell advance the state-of-the-art in strength analysis and predictive modeling of composite structures. In this contract, engineers at NSE Composites used advanced computer modeling techniques to evaluate the strength and durability of composite structural elements. The commercial finite element software, ABAQUS, was used together with advanced fracture mechanics approaches to predict the onset and growth of flaws or damage in the composite material when subjected to static or fatigue loading. The structural elements were then tested under the same loading to provide a comparison with the computer predictions. In support of the model development, element tests were conducted to provide baseline and validation comparison data.
BELL HELICOPTER – BJSFM
The overall objective of this project was to provide improved methods for bolted joint strength analysis, with emphasis on using the Fortran code, Bolted Joint Stress Field Model (BJSFM). Bell Helicopter selected a series of axial fiber, matrix shear, and transverse matrix failure criteria which NSE added to BJSFM under this project (Bell R&D criteria). NSE conducted an evaluation of BJSFM with the Bell failure criteria primarily through comparisons to ultimate strength and initial damage from notched test data of IM6/3501-6 tape laminates and study of predicted failure envelopes. To conduct the evaluation, NSE enhanced the Bell R&D BJSFM code to provide output files which can be easily read into spreadsheet programs. NSE generated predicted damage plots, failure envelopes, and other graphics for this report from the new output files. NSE also investigated alternate approaches for generating bolted joints strength, including different BJSFM methods, different d0 approaches, and maximum notched strength methods.
SBIR – BONDED JOINTS
NSE Composites performed a Small Business Innovation Research (SBIR) contract aimed at developing and implementing analysis methods for predicting strength and fatigue life of composite bonded joints in rotorcraft structures. NSE teamed with Bell Helicopter, Boeing, and Sikorsky to define and analyze three high-priority composite bonded joint configurations. Non-linear 2D finite element models were successfully used with strength-of-materials failure criteria to predict damage initiation, and with fracture mechanics methods to predict static strength and fatigue life. Fatigue life under spectrum loading was predicted using damage accumulation methods. Design and damage tolerance criteria were also addressed in the analyses.
Abstract
STTR – BOLTED JOINTS
NSE Composites performed a Small Business Technology Transfer (STTR) contract with the aim of making significant advancements in the understanding of composite bolted joints behavior. The STTR Phase II program involved a comprehensive approach to improving methods for predicting notched strength. This included an empirical evaluation of existing notched tension test data from DoD aircraft allowables programs, a static/ incremental x-ray test program, which included uniaxially notched tension and compression specimens in four aerospace layups, and development of analytical tools including progressive damage compression analyses.
Abstract