Typical Aerospace Projects
AERION SUPERSONIC – AS2 STRUCTURAL SIZING & CERTIFICATION
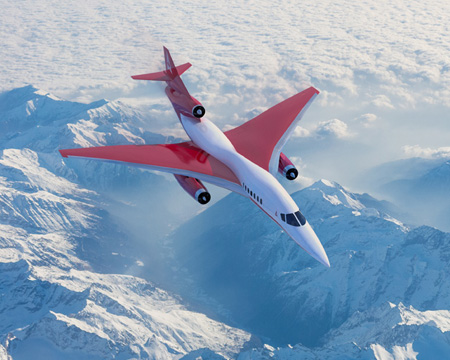
NSE Composites was contracted by Aerion Supersonic to provide technical consulting and engineering services in the areas of certification, testing, and analysis of primary composite structures on the AS2 supersonic business jet development program.
Specific areas of support included:
- Structural certification approaches, including guidance on design criteria, damage tolerance requirements, and top-level structural certification.
- Structural analysis methods development, including specialized buckling stability methods and approaches for post-buckling.
- Test and analysis, including guidance on the building block testing effort required for certification and validation of analysis methods and tools.
- Structural optimization, including optimization tools and approaches for large primary structures.
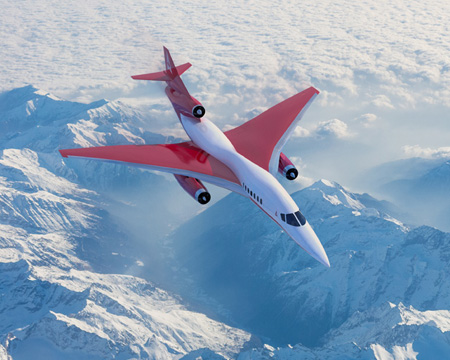
BOEING – 787 FUSELAGE AND WING DAMAGE TOLERANCE
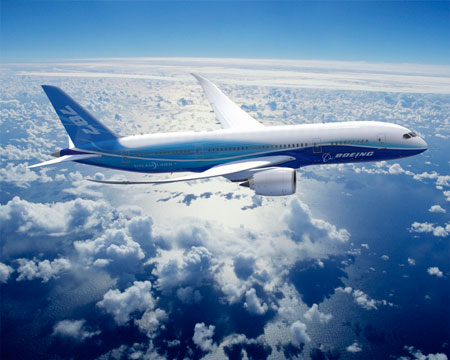
NSE Composites was contracted by Boeing to develop damage tolerance analysis methods for the 787 fuselage and wing structure. NSE combined Boeing’s test results from large-scale fuselage and wing test articles with predictions from finite element models to develop strength curves for the anticipated range of configurations on the airplane. These strength curves were then used to develop design guidelines for engineers to use when sizing the 787 structural components. In order to achieve a “damage tolerant” design, the tests and predictions included skin-stringer applications with large notches/damage. With this type of design, if structures such as the fuselage or the wing sustain damage, the aircraft can continue safe flight until the damage is inspected and repaired.
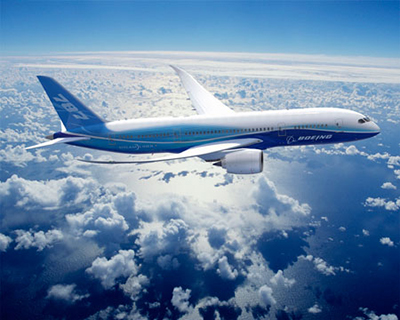
BOEING – 787 FUSELAGE SIZING AND OPTIMIZATION
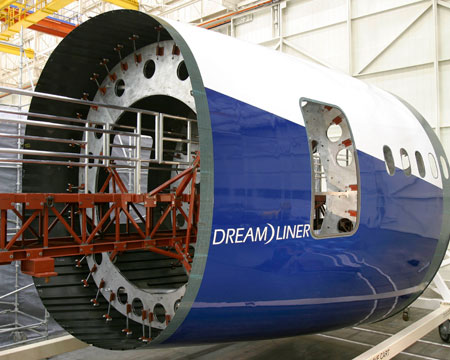
NSE Composites played a key role in the development of the composite fuselage optimization software that was used for the preliminary sizing of the Boeing 787. Many of the analysis routines were also used to generate the final structural margins of safety for the fuselage. The software uses numerous strength, stability, and durability analysis checks to provide optimum ply layups for every skin-stringer fuselage bay. Work included the development, validation, and software implementation of many new analysis methods. The software is based on COSTADE, “Cost Optimization Software for Transport Aircraft Design Evaluation,” which was originally developed as part of the NASA Advanced Composite Technology program.
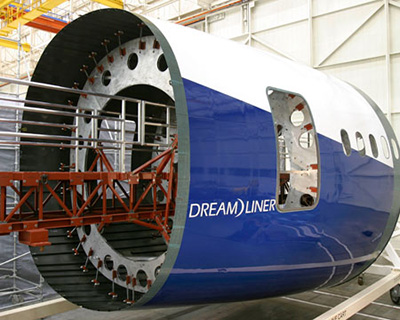
BOMBARDIER – CSERIES* AFT FUSELAGE STRUCTURAL ANALYSIS & CERTIFICATION
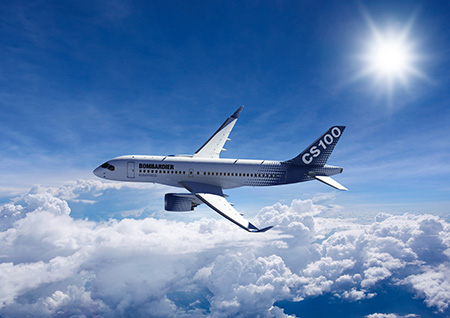
NSE Composites was contracted by Bombardier Inc. to provide engineering support and consulting related to the design, development, testing, and certification of composite structures on the CSeries aft fuselage and rear pressure bulkhead. Specific areas of support included:
- Structural analysis methods and strength allowables for bolted joints, buckling stability of skin-stringer configurations, and fracture-based delamination analysis
- Damage tolerance for large damage including criteria, testing, and analysis
- Building block test plan development, design criteria, and certification document review
* CSeries and CS100 are trademarks of Bombardier Inc. and/or its subsidiaries. Bombardier Inc. owns the copyright to the image of the CS100. Note that in 2018, Airbus purchased a majority stake in the CSeries program and the CS100 is now known as the Airbus A220-100.
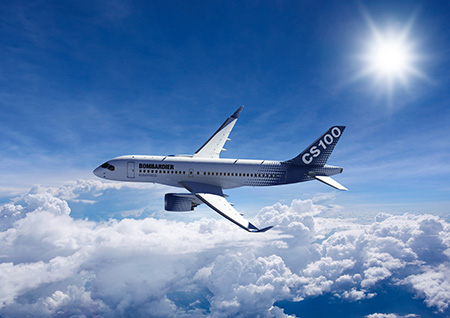
BOMBARDIER – LEARJET 85 STRUCTURAL ANALYSIS & CERTIFICATION
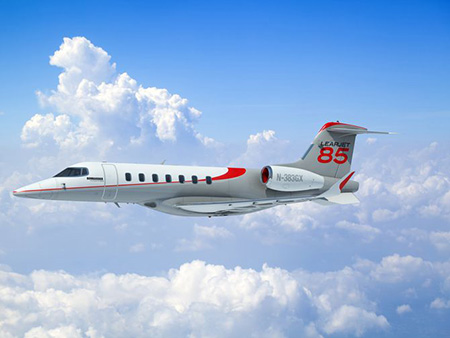
NSE Composites was contracted by Bombardier to provide engineering support and consulting related to the design, development, testing, and certification of composite structures on the Learjet 85 business aircraft. Specific areas of support included:
- Structural analysis methods and strength allowables including bolted joints, co-cured splice joints, and sandwich structures
- Damage tolerance for large damage including criteria, testing, and analysis
- Certification, building block test plan development, design criteria, and full-scale static and fatigue test sequencing
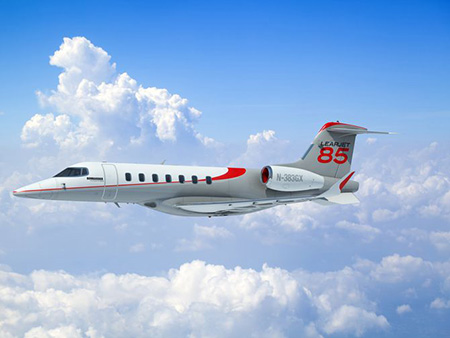
GE GLOBAL R&D – ENGINE FAN BLADE ANALYSIS
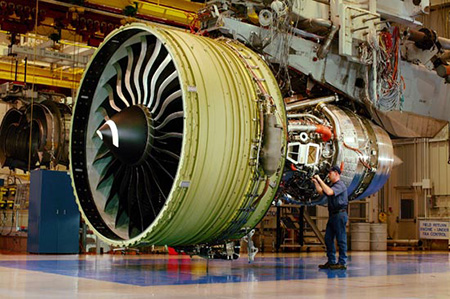
NSE Composites was contracted by General Electric (GE) Global R&D to perform detailed stress analysis and finite element modeling of composite engine blades to support design development and material selection. The analysis focused on interlaminar stresses, fatigue life predictions, and delamination growth. 2D and 3D non-linear models of selected details were developed using ABAQUS. Various design and test configurations were modeled to assess possible failure modes, quantify thermal residual stresses, and to improve designs. NSE also provided recommendations on material selection, test methods, test fixtures, and design configurations.
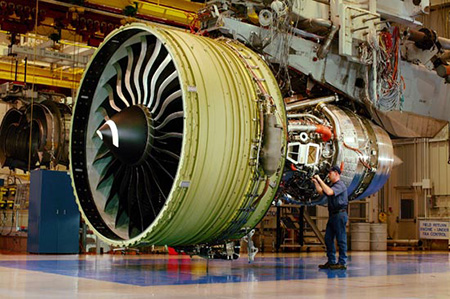
FAA – COMPOSITE SAFETY INITIATIVES
The Federal Aviation Administration (FAA) contracted NSE Composites to support two composite safety and certification initiatives: one on bonded joints, and one on damage tolerance and maintenance. In 2004, the FAA organized an effort to benchmark industry best practices for composite bonded structures. The primary objective was to document the technical details that need to be addressed for bonded structures, including critical safety issues and certification considerations. NSE Composites was contracted to:
- Collect information from past military and commercial applications of bonding to fabrication and repair of aircraft structures, with an emphasis on structural design and analysis.
- Document industry design practices and identify structural details crucial to analysis.
- Draft an expert opinion on the current state-of-the-art in using fracture mechanics for delamination and debonding modes of failure for bonded structures.
- Present at the ASTM/FAA Workshop on Computational Fracture Mechanics for Composites.
- Help define, organize, and run breakout sessions at the FAA Workshop for Bonded Structures. Present a summary of industry practices and technical issues related to composite bonded joints analysis, data, and substantiation.
In 2006 and 2007, the FAA held industry workshops to address safety concerns and technical issues for composite damage tolerance & maintenance. Discussion topics included: 1) factors affecting the substantiation of damage tolerance, including in-service maintenance, inspection & repair, 2) elements of safety management, 3) structural test protocols and supporting analyses, and 4) damage & defect types. In addition, the workshops helped to identify needs for new regulatory requirements and guidance. NSE Composites was contracted to:
- Help develop the detailed agenda, recruit presenters, and define a process for collecting participant inputs at the Composite Damage Tolerance & Maintenance Workshop.
- Support key workshop goals including identification of critical technical issues and areas of safety concern for damage tolerance & maintenance of composite structure on transport aircraft, identification of key similarities and differences in methods used to substantiate damage capability for transport aircraft composite structures.
- Identify and draft new content needed to update the Composite Materials Handbook (CMH-17) damage tolerance and supportability chapters and the FAA composites maintenance training standards.
- Help develop goals, strategies, agendas, and presentations for working group meetings with European Aviation Safety Agency (EASA), Transport Canada (TCCA), FAA, and selected industry participants.
PDS/ALENIA – 787 HORIZONTAL STABILIZER
NSE Composites was sub-contracted by PDS Engineering to help support Alenia Aeronautica in their development of the 787 horizontal stabilizer. Alenia fabricates this part of the airplane tail assembly from carbon/epoxy composite material. NSE performed specialized prediction analysis using finite element models of various parts of the horizontal stabilizer structure in conjunction with PDS’s developmental work of test plans for the program. Alenia combined the predictions from the computer simulations with the results from the testing to develop design guidelines for its engineers to use when sizing the full scale part.
BOEING – 737 STRUCTURES
Boeing Commercial Aviation Services contracted NSE Composites to develop improved analysis methods for assessing residual strength and designing repairs for damaged composite structure. These methods were then used to develop improved information for selected parts on the 737. Both the residual-strength and repair methods were developed in coordination with, and approved by, a company-wide team of experts and users to ensure they would be accepted for all airplane models. Both methods were then used to develop improved information for selected composite parts on the 737. The final repair layups, repair sizes, part zoning, and allowable damage limits were negotiated with the appropriate FAA Designated Engineering Representative (DER) for approval.
The residual strength methods, which are required to determine allowable damage limits for specific components, were based on an extensive test database. These test results were used to characterize the residual strength as a function of material, layup, damage size, and damage severity. Additional factors and techniques were developed to extend these data to a full range of realistic scenarios, including multi-site damage.
The repair methods were developed to determine the number of repair plies necessary to return a damaged part’s capability. These methods address all relevant failure modes and include the effects of original and repair material, as well as any possible increased loads attracted to the region as the repair’s stiffness is increased. Maximum size limits were also developed based on a substantial test database.